Added a rubber band to keep things in place on port tack.
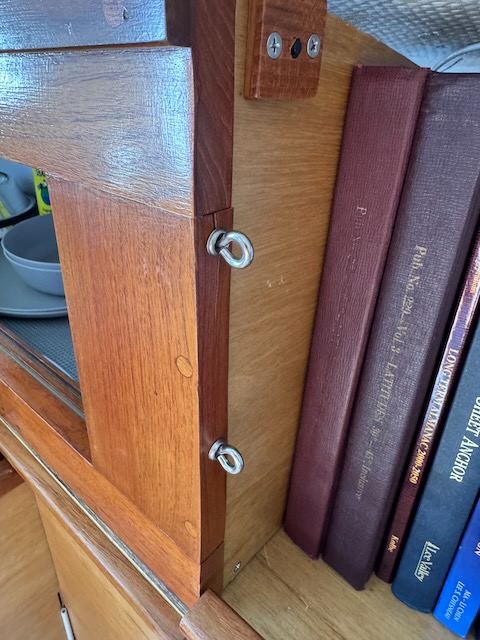
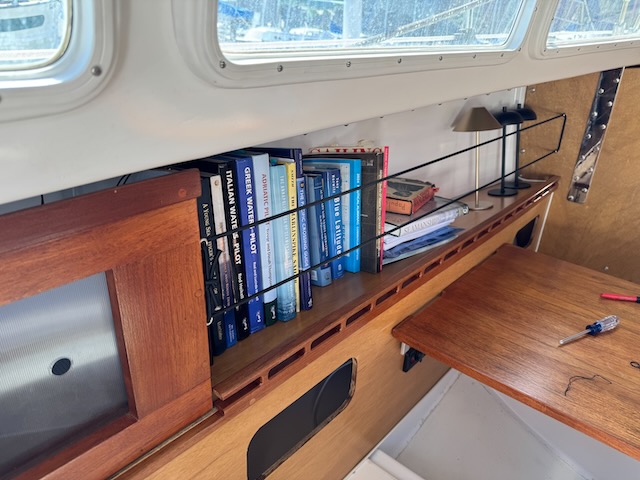
1971 Newport 30 Sailboat
Was a bit tricky as I wanted to get all 4 sides. Using SeaGold really helped as it dries quickly.
Managed to avoid heavy runs or drips. Love that chocolate teak color in matte!